Husky launches hot runner controller for two to 128 zones
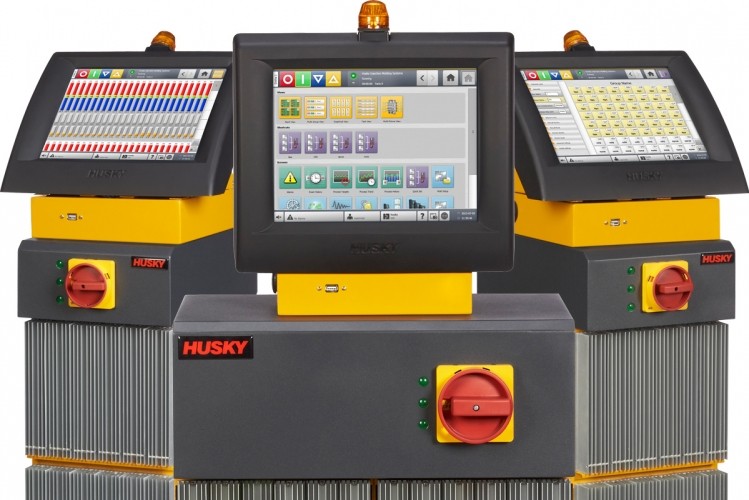
The Altanium Delta3 controller is positioned as a mid-range operator interface designed to bridge the gap between the Neo2 and Matrix in price and functionality, the firm told FoodProductionDaily.com.
Delta3 offers an integrated platform for two to 128 zones of control and helps customers achieve increased part quality and improved uptime.
“Based on the two-zone design of the cards, Delta3 is capable of providing from two to 128 zones of control. This means that it is suitable for any hot runner application that does not require more than 128 zones,” explained Matthew Cummings, Husky’s product manager for Altanium.
Improved methods
Delta3 has an improved navigation method coupled with a large, full color touchscreen which shortens the learning curve for new users and ensures fast and consistent start-ups.
Automatic storage and recall of set-ups ensure the same processing parameters are used for a mold without operator intervention. Multilingual support increases user adoption while historical event auditing and enhanced process monitoring enables fast and accurate troubleshooting, said Husky.
Altanium controllers use Active Reasoning Technology (ART), providing optimized control for shot-to-shot and cavity-to-cavity consistency and repeatability.
The firm said for injection molded parts, Delta3 provides similar benefits to the packaging industry as other industries.
Eliminate risk
Delta3 has monitoring capability to further eliminate the risk of bad parts entering the downstream process. Integrated mold protection prevents material degradation and addresses issues before part quality is compromised to decrease downtime and reduce risk during operation.
Cummings said there are times when it is necessary for the controller to stop heating the mold or circumstances that require the machine to stop cycling.
“If this occurs, the material could degrade putting the mold at risk or allowing bad parts to enter the downstream process.
“The best way to protect against damage or defective parts from entering the supply chain is a closed loop interlock circuit that ensures the controller and machine are in constant communication.”
Delta3 provides at-temperature output, PCM output and remote standby input to mitigate risk.
This connectivity enables both pieces of equipment to make informed decisions, based on the state of the other, which ensures the integrity of the mold and part quality, he said.
Integrated control card design also minimizes discrete connections and components and Altanium control cards contribute to lower operating costs while allowing for flexibility to grow with changing production needs.
“The fundamental Altanium design simplifies integration into the production line by utilizing a single 16 amp card type that allows the controller to run any conventional hot runner system, regardless of what order the tip and manifold zones are arranged,” said Cummings.