Guest article
Sustainability in troubling times
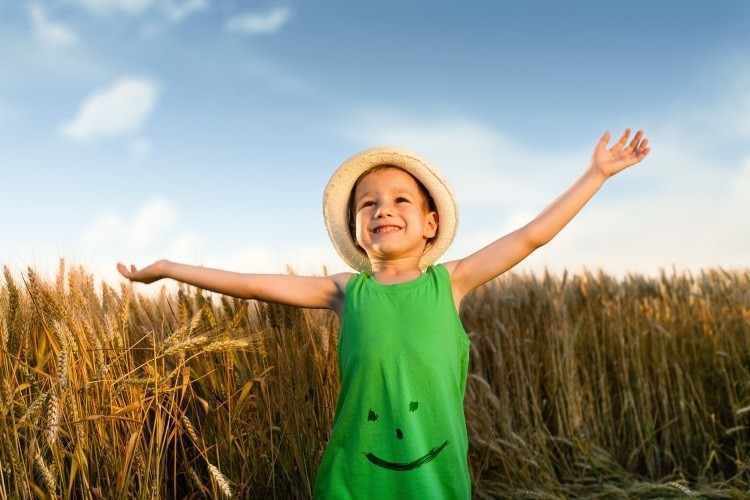
Hoping for the best, but planning for the worst should be part of every company’s business strategy.
Although none of us could have imagined a global pandemic and the ensuing personal and business challenges that it would bring, there is a lot that companies can do to build sustainability into their production processes, as well as into the products they manufacture.
Developing robustness in the supply chain
As a global provider of functional ingredients, we at BENEO have been very aware of the potential vulnerabilities that can occur due to issues such as reduced harvests. Although, as with any fresh, raw ingredient, it is difficult to create significant stockpiles, we do however have ‘safety stock’ levels in each of our production plants. This allows us to ensure that supply to food and beverage producers remains uninterrupted in the short-term, even if there are disruptions to the harvest or distribution chain.
To bring even more robustness to our ingredient production process, the decision was taken years ago to grow our base ingredients across equators where possible.
This mitigates the damage of climate variations, maximising the benefits of each country’s specific growing conditions, as well as reducing transportation distances to ‘local’ markets. For example, our Orafti Inulin and Oligofructose ingredients, which are derived from chicory root, are grown in both Belgium and Chile.
Although none of us could have foreseen the disruption of a pandemic, by thinking outside the box when it comes to ingredients sourcing and storing, it is possible to build more sustainability into the production process.
Sustainable and secure production
In order to ensure the smooth transportation of crops to our factories, we aim to keep the distance between our factories and fields as small as possible and use alternative means of transport wherever we can. For instance, we now make 2,500 fewer truck journeys per year than we used to, while still carrying the same volume of ingredients and raw materials, due to our increased use of barges.
Another way we have sought to build robustness into our supply chain is by making a strong commitment to building long-term relationships with suppliers, customers and employees.
In Chile, our harvest season began at virtually the same time as the country went into lockdown as a result of the pandemic. To secure raw material supply and production, our farmers and their workers have extended harvesting times to get the crop in and we have worked with them to increase transport provisions, enabling social distancing to be maintained. As a result, we have been faced with minimum interruption to our operations during this difficult pandemic season.
Investing in supplier and employee relationships isn’t a ‘quick fix’ but one that reaps significant rewards, especially in challenging times.
Planning for the future
The pandemic has reminded us that we can’t control everything. However, we can and should – as food and beverage producers – be playing our part in investing in the future. For BENEO, this means implementing a range of corresponding initiatives.
We have spent the last 30 years focusing on bringing energy efficient processes to our production sites. As a result, we have been able to reduce specific energy consumption by 50% over that time. Examples are the installation of a biomass boiler in our factory in Chile, having a high level of cyclical water usage across all the production plants and focusing on increasing our use of renewable energy.
As a business based on agricultural crops, we also invest heavily in the soil that are farmers use. BENEO’s Agronomy department works closely with the contract farmers to manage the long-term health of their soil and to prevent over-fertilisation or soil exploitation and soil erosion.
These measures, and many more, are not designed to give us quick returns. They have all been put in place to ensure that the company isn’t just robust for today’s challenges, but is equipped to face the ones to come as well.
Having a robust and flexible production process isn’t necessarily quick to achieve, but the rewards of operating a sustainable business far outweigh the costs. Although building more robustness into production processes takes commitment and time, in these increasingly turbulent operating conditions, it has been shown that sustainability has become a necessity.
BENEO is a division of the Südzucker Group that employs more than 1,000 people in production units in Belgium, Chile, Germany and Italy. Its functional ingredients are derived from chicory roots, beet sugar, rice and wheat, to help improve a product nutritional benefits, like ‘less fat’, ‘less sugar’, ‘less calories’, ‘added fibre’ and ‘gluten-free’.